As markets grow and production demands increase, factory liquidation has become a critical component of effective asset management for businesses. To ensure a smooth and transparent liquidation process, companies must adhere to legal regulations and develop a clear, detailed plan. In this article, we will guide you through the factory liquidation process and highlight essential considerations to help you avoid pitfalls and maximise returns.
Distinguishing Between Asset Liquidation and Asset Transfer
In business operations, effectively managing and utilising fixed assets (FA) is crucial for optimising costs and increasing production efficiency. However, not all fixed assets maintain their usefulness or economic value over time. In such cases, businesses may need to either liquidate or transfer these assets. Below are the key differences between asset liquidation and asset transfer:
Asset liquidation is the process of selling or disposing of fixed assets that are damaged, no longer usable, or obsolete in terms of technology, making them unsuitable for the company’s current production needs. Typically, the cost of repairing or maintaining these assets outweighs the economic benefits they could provide.
Asset transfer, on the other hand, refers to the sale of fixed assets that the business no longer requires or deems economically inefficient to use. Transferred assets are often still in good working condition but are no longer aligned with the company’s business strategy or operational model.
The Benefits of Liquidating Old Factories
Liquidating old factories provides businesses with several key benefits, including generating additional income, reducing costs, ensuring safety, and contributing to environmental protection and employee health. This is not only an economic solution but also a corporate social responsibility that promotes sustainable and healthy community development. Specifically:
– Generating income through liquidation: During operations, businesses often face the need to demolish, rebuild, or relocate factories and warehouses to meet changing market demands. These processes can be costly and financially challenging. However, by liquidating old factories in Hanoi, including selling any remaining valuable scrap materials, companies can generate a new stream of income. This revenue can be reinvested into other activities, improving cash flow, and reducing financial pressure.
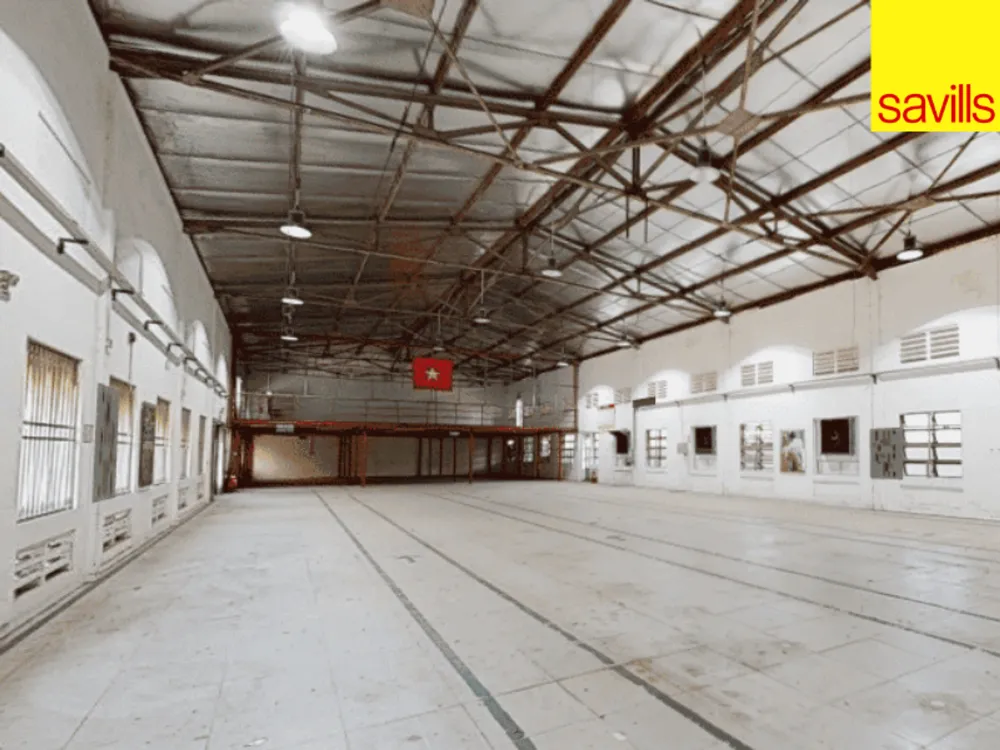
Liquidating old factories provides businesses with the funds to support their operational activities
– Cost savings and safety assurance: Demolishing and handling old factories requires specialised labour and equipment, making the process expensive and complex. By utilising factory dismantling services, businesses can significantly reduce costs. These service providers manage the entire process, from dismantling and transporting to scrap processing, allowing companies to simply supervise without direct involvement.
-Reducing pollution and minimising environmental impact: Old factories and unused scrap materials can become a source of dust and provide a breeding ground for insects and other harmful elements. If not promptly addressed, these materials can decompose, leading to pollution and negatively impacting the workplace environment. This not only decreases productivity but also directly affects employee health.
Factory Liquidation Process in Vietnam
To effectively conduct the process of disposing of fixed assets, businesses should follow these steps:
– Step 1: Prepare a Fixed Asset Disposal Proposal
The process starts with the business preparing a disposal proposal, detailing the characteristics, and listing the fixed assets to be disposed of. Following this, the management will issue an official decision on the disposal and authorise a responsible person to manage the process.
– Step 2: Form a Disposal Committee
A disposal committee is established, consisting of individuals with in-depth knowledge of the fixed assets. This committee will be responsible for inspecting, evaluating, and executing the disposal process in line with current regulations.
– Step 3: Conduct the Disposal of Fixed Assets
The disposal committee will take the necessary steps to dispose of the assets, including preparing a disposal report. This report will outline the method of disposal, whether through sale or destruction, depending on the specific circumstances.
Read the latest industrial property lease termination report to ensure legal compliance during the asset disposal process.
– Step 4: Complete the Disposal Process
Once the disposal is complete, the committee will prepare a fixed asset disposal report to ensure transparency and accuracy in the transaction.
Important Considerations When Buying or Selling Liquidated Industrial Property
When buying a used factory, businesses should carefully consider several crucial factors to ensure the purchase is both reasonable and beneficial for business operations.
– Factory Condition and Location:
Evaluating the condition and location of a used factory is crucial. A thorough inspection of the existing infrastructure and equipment within the factory is necessary to ensure that the liquidated factory in Ho Chi Minh City meets both the current and future production needs of the business. Additionally, the factory’s location must be considered, as it directly impacts logistics, transportation, and overall convenience for the company.
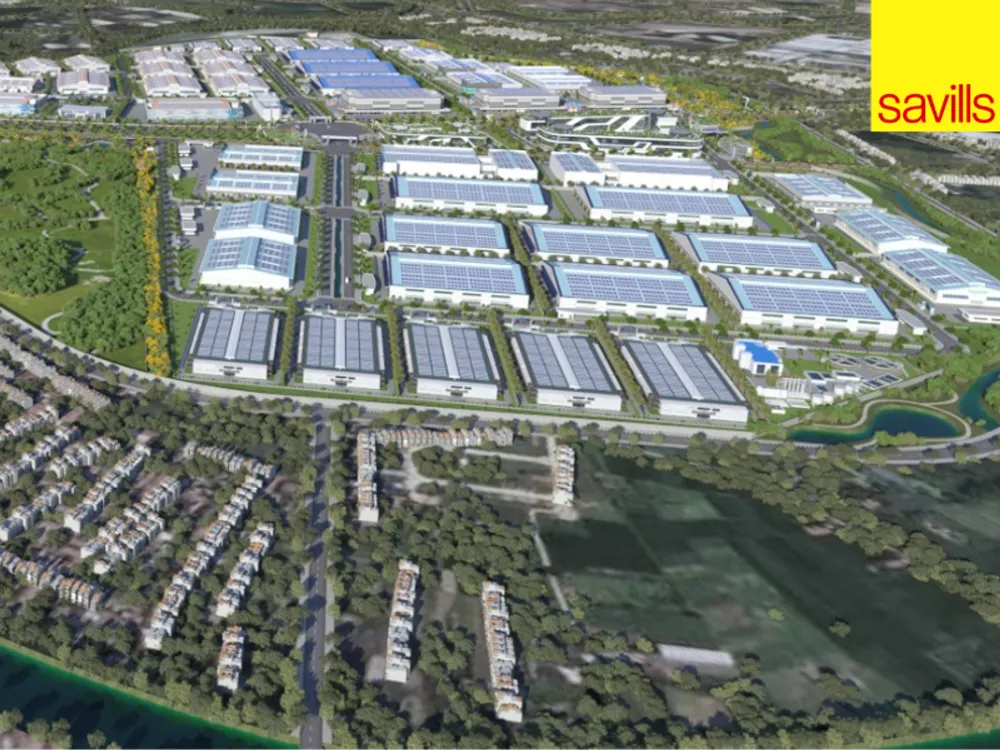
Businesses must thoroughly verify the origin, location, and condition before purchasing a used factory
– Factory Origin:
Before deciding to purchase a used factory, it is essential to thoroughly check the legal status and ownership to ensure there are no legal complications that could affect the transaction. Additionally, investigating the factory’s usage history helps assess its wear and tear and its potential for reuse.
– Factory Quality:
Carefully inspect the structure and building materials of the factory to ensure they meet safety and durability standards during future use. Evaluating the technical systems such as electricity, water, and fire safety is also crucial to prevent unexpected production disruptions.
How to Determine the Price of a Liquidated Used Factory
The purchase price of a used factory is not set and can fluctuate depending on several factors within the scrap market. This market is influenced by supply and demand, pricing, and quality standards, making the purchase price subject to change over time. It requires careful consideration of specific market conditions.
Key Factors Affecting the Liquidation Price of a Factory:
– Factory Size and Structure
– Location of the Factory
– Level of Deterioration
– Quantity and Quality of Scrap
– Reuse Potential of the Factory and Scrap Materials
Leasing old factories with Savills Viet Nam
Savills Viet Nam is one of the leading real estate service companies in the country, with a strong presence and reputation in the market. We take pride in offering high-quality, flexible, and tailored solutions for industrial factory leasing to meet the specific needs of each client.
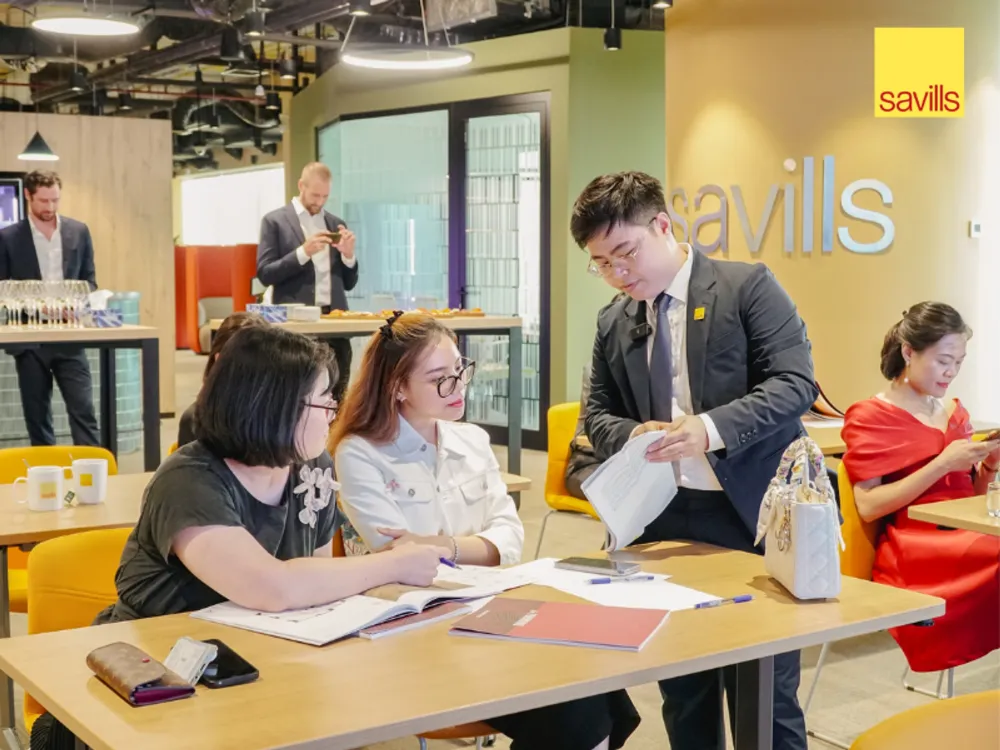
Savills Industrial provides leasing services for factories in Vietnam’s leading industrial parks
Savills Industrial offers factory leasing services in Viet Nam that not only meet your production space needs but also enhance business efficiency for enterprises. With an extensive network, we provide a diverse selection of customisable factory options in various sizes, strategically located in both industrial parks, and developed industrial areas. Optimise your operations with our premier factory leasing solutions today.
If you are looking for suitable production or storage space for your business, please contact us today at our hotline: 0986.718.337 – Mr John Campbell for detailed advice and support regarding Savills Vietnam’s factory leasing services.